Myarm 300 Pi: A Leap From 6 Dof To 7 Dof Robotic Arm
About the project
Discover the Future of Robotics: Introducing the myArm 300 Pi, a 7-Axis Robotic Arm.
Project info
Difficulty: Easy
Platforms: Raspberry Pi, ROS, Elephant Robotics
Estimated time: 1 hour
License: GNU General Public License, version 3 or later (GPL3+)
Items used in this project
Hardware components
Story
In the rapidly evolving world of technology, our relentless pursuit of innovation and excellence drives us to meet our customers' needs and exceed their expectations. Today, we are delighted to announce our latest product - the myArm 300 Pi, a 7-DOF desktop robotic arm. What sets this product apart is its flexibility and programmability, as well as its choice of working radius and embedded control board. In this article, we will provide a comprehensive introduction to the features and functionalities of the myArm 300 Pi, and compare it to our 6-DOF robotic arm, It will offer you a deeper understanding of our new product and how it can effectively cater to your specific requirements.
myArm 300 PiThe myArm 300 Pi is a brand new 7 DOF collaborative robotic arm with a symmetrical configuration. Its design style continues the compact and lightweight features of the myCobot series. Equipped with 7 high-precision servo motors, the myArm has a maximum working radius of 300mm and a maximum payload capacity of 200g at the end effector. It achieves a high repeatability positioning accuracy of up to ±0.5mm.
The control board of the myArm 300 Pi adopts the Raspberry Pi 4B 4G, which is a widely recognized mini-computer renowned for its exceptional performance and versatile programming environment.This integration allows users to exert control over the myArm 300 Pi using an array of programming languages, including Python, C++, Java, and etc. This feature greatly enhances user convenience and flexibility.Additionally, the myArm 300 Pi support ROS1/ROS2 providing many functionalities in the ROS operating system, such as path planning, obstacle avoidance, 3D perception, and more.
Perhaps you might question the necessity of a 7 DOF robotic arm when a 6 DOF robotic arm already emulates the joints of a human arm.Let's delve into the reasons behind the requirement for a 7 DOF robotic arm.
What are the difference between 6 DOF and 7 DOF robot arms?In the following section, we will primarily highlight the differences between 6 DOF and 7 DOF robotic arms from 4 aspects.
1. DOF(degree of freedom)As the name implies, a 7 DOF robotic arm features an additional movable joint compared to a 6 DOF robotic arm.Generally, a 6-DOF robotic arm possesses the minimum DOF required to accomplish its tasks. 3 DOF are utilized for spatial positioning, while the remaining 3 DOF are used for orienting the end effector. On the other hand, a 7-DOF robotic arm is considered a redundant robot, meaning it has more DOF than the minimum required to complete a specific task. In addition to the 3 DOF used for positioning and 3 DOF used for orientation, the extra DOF in a 7-DOF robotic arm is typically employed to provide increased flexibility and freedom of movement.
2. Complex Trajectory MovementOne of the key distinctions between these two types of robotic arms is that a 7DOFs robotic arm has the capability to perform complex movements and switch to another configuration while maintaining the three-dimensional structure of the end effector. In contrast, a 6 DOF robotic arm lacks this capability. When a 6 DOF robotic arm operates in the same position, there are instances where the entire arm may twist to the other side.
Just as shown in the illustration, mycobot 280 only undergoes a translation in coordinates, but the overall structure of the robotic arm undergoes a significant transformation.This is a result of the limitations of the 6 DOF robotic arm.
Let's take a look at the performance of the 7 DOF robotic arm.
This particular motion demonstrates the unique trajectory that a 7 DOF robotic arm is capable of. Another term for this is a redundant robotic arm, as it allows for significant changes in the overall arm configuration while maintaining the end effector's coordinate position. These complex movements are beyond the capabilities of a 6 DOF robotic arm. Additionally, there are certain special actions that can only be accomplished by a 7 DOF arm, such as the expandable trajectory shown in the diagram. This empowered myArm to operate in narrower and more complex environments.
Both 6 DOF and 7 DOF robotic arms can handle most scenarios, including industrial production, logistics and warehousing, medical fields, research and development, service industries, education, and more. However, in specific environments, the utilization of a 7 DOF robotic arm may be more suitable, primarily due to its greater flexibility and more complex motion capabilities.
● Complex Path Planning: In cases where precise movement along a specific path is required, such as complex curves or around obstacles, a 7 DOF robotic arm may have an advantage over a 6 DOF robotic arm. Because the additional DOF enables the arm to operate in more intricate environments.
● Space Utilization: In environments with limited space, such as compact workstations or crowded factory settings, a 7 DOF robotic arm can better utilize the available space and perform more complex tasks. The extra joint allows the arm to assume additional positions and perform a broader range of tasks within the confined area.
● Precision Operations: In applications that require precise operations, such as minimally invasive surgery or assembly of microelectronic devices, a 7 DOF robotic arm may offer advantages over a 6 DOF robotic arm. The additional joint provides more precise control, enabling the arm to perform finer operations.
● Obstacle Avoidance: The additional DOF in a 7 DOF robotic arm allows for better task completion in scenarios that require obstacle avoidance. For example, in complex factory environments or medical settings where surgical procedures need to be performed around the human body, a 7 DOF robotic arm can navigate more effectively.
4.Control and programmingControl
From the perspective of forward and inverse kinematics, forward kinematics is the process of calculating the position and orientation of the robotic arm's end effector given the specified joint angles. In both 6 DOF and 7 DOF robotic arms, forward kinematics can be solved relatively directly using geometry and trigonometric functions.
Inverse kinematics, on the other hand, refers to the process of calculating the required joint angles given the target position and orientation of the robotic arm's end effector. For 6DOFs robots, inverse kinematics problems usually have a unique solution (although there may be multiple or no solutions at certain positions). However, for 7DOFs robots, due to the additional DOF, inverse kinematics problems may have infinitely many solutions. This requires the use of optimization methods or heuristic approaches to select the optimal solution, such as minimizing joint motion, avoiding joint limits, or satisfying other specific constraint conditions. Therefore, it is much more complex than for 6DOFs robotic arms. More DOF mean more complex control strategies, design and manufacturing, computational requirements, and so on.
Programming
mycobot280 and myArm300 are compatible with various programming environments. They not only support the ROS environment but can also be controlled using Python. You can choose the programming platform you are familiar with, eliminating the need to spend a lot of time learning a new programming language.
Elephant Robotics strives to provide users with more possibilities. Development can be done on various platforms, and many control interfaces, such as torque and force parameters, are open for customization.
SummaryAfter comparing the performance and functionality of 6-DOF and 7-DOF robotic arms, we can see the outstanding features of the myArm 300 Pi 7-DOF robotic arm. One notable advantage of a 7-DOF robotic arm is its enhanced flexibility and DOF, allowing it to work in more complex and narrow environments and perform more complex tasks. In contrast, although 6 DOF robotic arms have proven to be sufficient in many applications, the advantages of a 7-DOF robotic arm become apparent in specific scenarios, such as the need for precise operations within confined spaces.
Furthermore, the Raspberry Pi control board, open control interfaces, and ROS robotic operating system of the myArm 300 Pi 7-DOF robotic arm surpass traditional 6-DOF robotic arms in terms of programming flexibility and expandability. These features make the myArm 300 Pi suitable not only for traditional mechanical operation tasks but also for advanced robot research and development.
We hope that more users can create more interesting and meaningful projects with myArm 300 Pi. If you want to learn more about myArm 300 Pi, please click the link. If you have any suggestions, please leave a comment below. If you liked this article, please give us a thumbs-up!
Credits
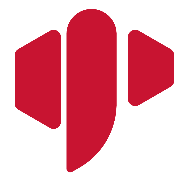
Elephant Robotics
Elephant Robotics is a technology firm specializing in the design and production of robotics, development and applications of operating system and intelligent manufacturing services in industry, commerce, education, scientific research, home and etc.
Leave your feedback...