A Good Helper For Grabbing Targets For Your Cobot | Electric
About the project
Two different electric grippers with myCobot 320
Project info
Difficulty: Easy
Platforms: Elephant Robotics
Estimated time: 1 hour
License: GNU General Public License, version 3 or later (GPL3+)
Items used in this project
Software apps and online services
Story
This article will discuss two electric grippers with the myCobot 320. We will talk about their functions and which suits your project better.
GripperWhat is a gripper?The gripper of a robotic arm, also known as one kind of end-effectors, is mounted on the arm and able to grab, transport, and place items into a particular location.
Based on the manufacture, the gripper is like a human hand, such as a three-finger or five-finger product. Or a palm without fingers, such as a parallel two-finger gripper. They can be tools for carrying out specialist work, such as a spray paint gun mounted on a robot's wrist, welding tools, etc.
In terms of driving methods, there are three types of driving: hydraulic, pneumatic, and electric.
Hydraulic end-effector owns easy speed regulation but higher pressure, high system cost and more troublesome maintenance.
Pneumatic end-effectors are currently the most widely used end-effectors in the industry due to their low cost and wide range of models. Still, the unstable output of air pressure from the air source can lead to insufficient clamping force, making the workpiece prone to falling off.
Electric end-effectors are superior to hydraulic and pneumatic end-effectors in terms of performance and structure and are the future trend in the end-effector industry.Compared to pneumatic end-effectors, the system structure replaces the pneumatic end-effector's air source, filter, solenoid valve and other parts with an electric drive. Compared to the hydraulic end-effector, the system is easy to maintain and does not require the use of hydraulic energy, which reduces energy pollution.
Today we are presenting a electric parallel gripper and an adaptive gripper.
Here is an abbreviated list of the specification of this two grippers.
We use the myCobot 320 to connect to these two grippers.
myCobot 320 is a six-axis robotic arm with a wide range of functions that can be equipped with various actuators, such as grippers, suction pumps, etc. It is particularly suitable for education and research.
Here is a video demo of the electric gripper.
According to the specification, the stroke of the adaptive girpper is 0 to 90 mm.
As we can see the adaptive gripper have a wide range of gripping possibilities and can easily pick up less conventional objects. Here are the detailed parameters and construction of the adaptive gripper.
Structure of Adaptive Gripper
Structure of Adaptive Gripper
(The diagram of the gripper structure gives the user a better understanding of its composition, how it is driven, etc.)
Electric Parallel GripperIn contrast, the electric parallel gripper has a clamping width of only 14 mm, but it is more accurate and stable than the adaptive gripper. The electric parallel gripper is more suitable for scenarios where high precision is required and parts are small.
After watching the demonstration in the video, you may wonder what the advantages of the electric parallel grippers are when the adaptive grippers can also do the same.
The advantage in terms of clamping width is lost in exchange for the high accuracy of ±0.02mm and the ability to clamp quickly. Its advantages are demonstrated in some assembly work.
Here are the detailed specification and construction of the electric parallel gripper.
Structure of Electric Parallel Gripper
Structure of Electric Parallel Gripper
SummaryThe choice of a suitable gripper depends on the environment in which it is used. If you are using a large object (width>14mm), then you can choose an adaptive gripper. If you are using an object that requires a more accurate gripper (e.g., assembly work), then choose an electric parallel jaw. To find out more about the myCobot 320, please click on. We'll update the pneumatically driven flexible gripper and suction pump later. Your likes and comments are our motivation!
Credits
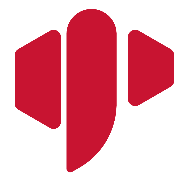
Elephant Robotics
Elephant Robotics is a technology firm specializing in the design and production of robotics, development and applications of operating system and intelligent manufacturing services in industry, commerce, education, scientific research, home and etc.
Leave your feedback...